Modern-day automation has transformed manufacturing and production in various industries, including the automotive, food and beverage, pharmaceutical, and packaging sectors. At the heart of this automation are gear motors, which are used in various applications, including conveyor systems, pumps, and mixers, among others. In this blog article, we will take a deep dive into gear motors, focusing on parallel gear motors and how they are crucial components in automation.
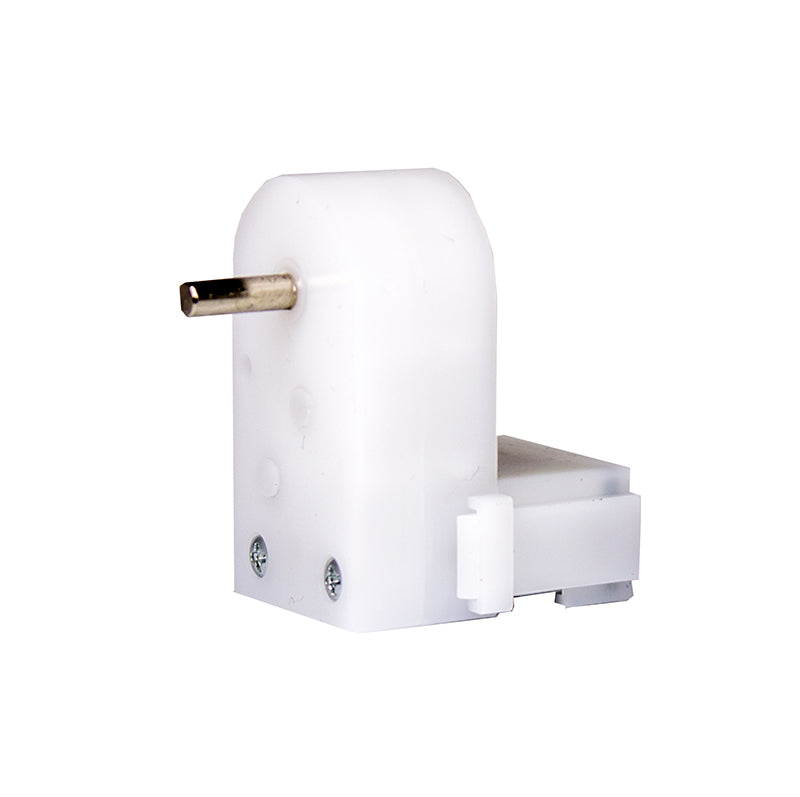
What are Gear Motors?
Gear motors are electric motors that are designed to work in combination with gear reducers (also referred to as gearboxes or speed reducers) to reduce motor speed and increase torque. The gear reducer helps to match the motor's speed to the desired output speed, which is essential for producing a smooth and controlled operation. Gear motors can be classified according to the type of gearing used, which could be helical, spur, planetary, or worm.
Parallel Gear Motors
Parallel gear motors are a type of helical gear motor that has parallel output and input shafts. They are commonly used for horizontal or inclined conveyor drives, and their design makes them suitable for use in applications where space is limited or where motor mounting is limited. Parallel gear motors come in a wide range of sizes and power outputs, making them versatile and used in various machinery and equipment.
How Parallel Gear Motors Work
Parallel gear motors function in the same way as other helical gear motors, which have a set of helical teeth that are cut into the gear's circumference. When the gear motor is in operation, the power is transmitted from the motor's input shaft down to the gear reducer. As the motor turns, the gear reduction system slows down the rotation speed and increases torque, which then powers the parallel output shaft.
Benefits of Parallel Gear Motors
Parallel gear motors have several benefits that make them the preferred option for various applications:
1. High Efficiency: Parallel gear motors have high efficiency, making them suitable for applications that require accurate speed control.
2. Compact Design: Parallel gear motors have a compact design, making them suitable for use in applications where space is limited.
3. Low Noise Level: Parallel gear motors have a low noise level, making them ideal for use in environments where noise pollution is a problem.
4. Low Maintenance Costs: Parallel gear motors have a low maintenance cost, reducing the total cost of ownership.
Applications of Parallel Gear Motors
Parallel gear motors are used in various applications, including:
1. Conveyor Systems: Parallel gear motors are used in conveyor systems such as textile machinery, automatic car washes, and food processing systems.
2. Mixers: Parallel gear motors are used in mixers such as paint mixers, food mixers, and pharmaceutical mixers.
3. Pumps: Parallel gear motors are used in pumps such as chemical pumps, hydraulic pumps, and vacuum pumps.
Conclusion
Gear motors are crucial components of modern-day automation, and parallel gear motors are the preferred option for various applications. Their high efficiency, compact design, low noise level, and low maintenance costs make them suitable for use in various industries. As automation continues to grow, parallel gear motors will remain a key component, ensuring the smooth and efficient operation of machinery and equipment.